IN-CIRCUIT TEST DEVELOPMENT SERVICES
FAST, HIGH QUALITY AND ON-TIME ATE TEST DEVELOPMENT
ATE Platforms Supported
- Keysight 3070
- Teradyne TestStation, Spectrum & Z18xx
- Acculogic Flying Probe & MDA Systems
Every day, test engineers are required to develop and support manufacturing test requirements. By relying on Acculogic, they free themselves from the hassles of in-circuit test development and test fixture design – the same way we have done for industry leaders in aerospace, defense, telecom, and more. And you can take advantage of this too.
The Acculogic TPS team specializes in creating custom test programs
Test Coverage Analysis: The team performs detailed analysis to ensure that the test programs provide optimal fault coverage, identifying and addressing potential areas of concern on the PCB.
Programming and Test Algorithms: The TPS team designs and develops software programs that run on Acculogic’s test systems, ensuring that each PCB is tested thoroughly and efficiently.
Component Library Management: The TPS team maintains a comprehensive library of components, which helps in accurately testing different parts of the circuit board without requiring constant reprogramming.
In-Circuit Test Development Services Offered
- Test program development
- Fixture design & fabrication
- Design for testability and CAD analysis
- Library model development
- Boundary Scan test development
- FLASH, E2PROM and ISP/ISC programming support using ICT and Boundary Scan
- Combinational tests: In-Circuit/ Functional/Boundary Scan (JTAG)
- Detailed test coverage report
- On-site / remote installation
- After-sales technical support
- Engineering consulting services
ATE Platforms Supported
Your Goal Is to Ship Quality Products On-Time and Within Budget. We Have a Way to Get You There.
We’ll give you the support you need to quickly get your production test requirements converted to production test solutions.
Acculogic’s In-Circuit Test Development Services offer manufacturers a comprehensive solution to ensure the quality and functionality of their PCBs. With their expertise in custom test development, high fault coverage, and the ability to reduce production time and costs, Acculogic helps manufacturers achieve faster time-to-market and higher first-pass yields. Their flexible, scalable, and cost-effective ICT solutions make them a valuable partner in electronics manufacturing, whether for high-volume production or low-volume, high-complexity produ
Industries Served
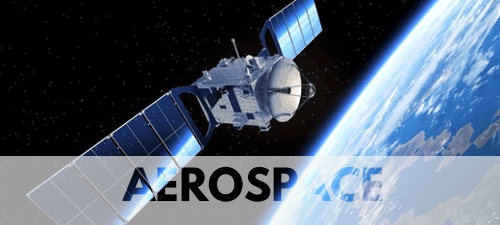
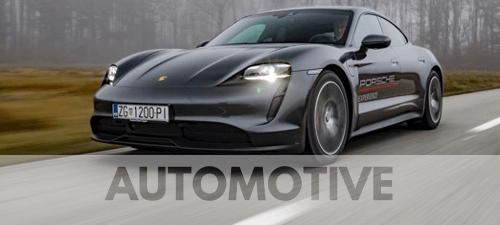
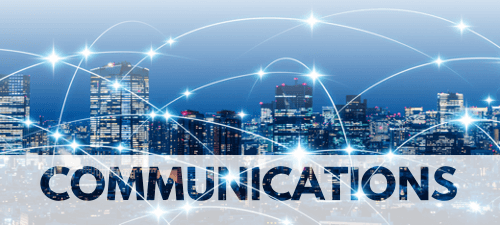
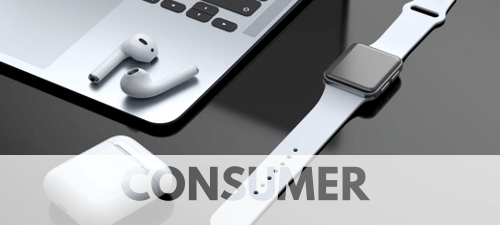
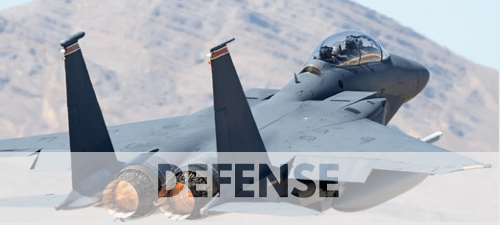
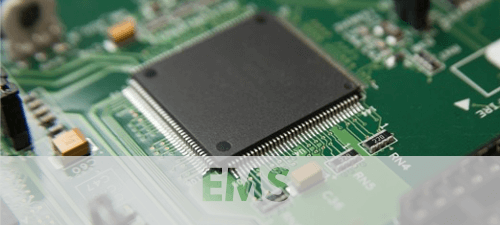
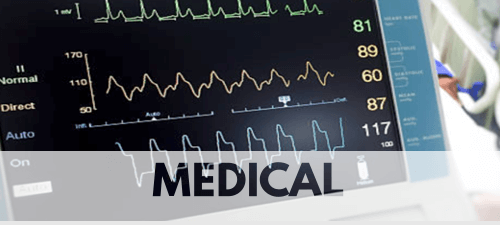
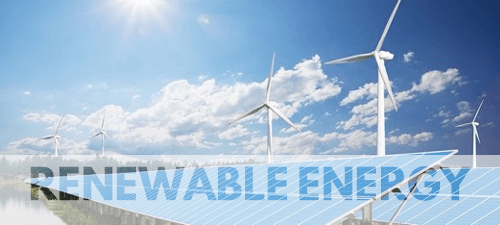
Sample Test Fixtures
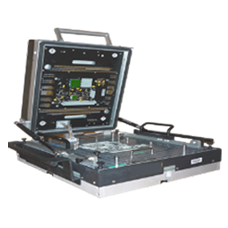
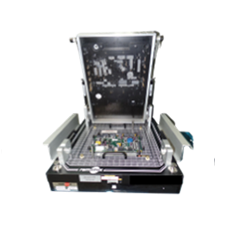
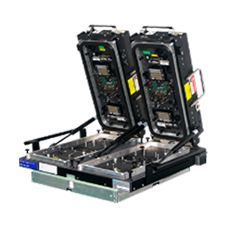
Dual-well test fixture